Some Answers for the Doubts Regarding Magnet Coating and Plating
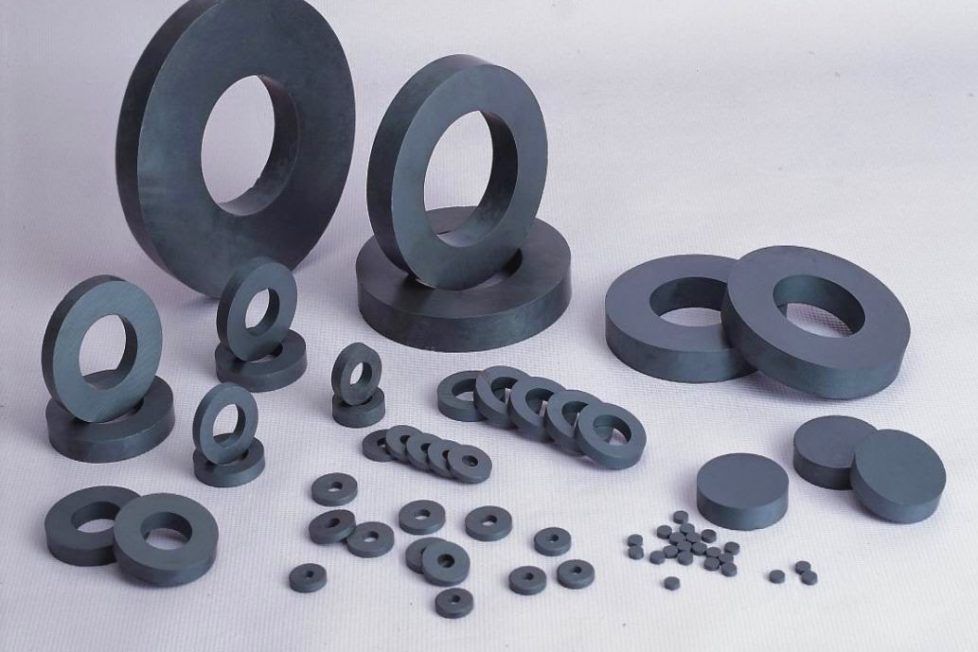
There are many magnet types available naturally from the earth’s crust. There are even some magnet types manufactured using the chemical composition of the naturally available magnets. Every magnet requires outer coating so as to protect it from damaging or even corroding due to external influence.
When it comes to magnetic coating, there are many questions that usually pop up in the mind of people, who frequently work with magnets. Some are listed below.
When is the right time to coat Sm-Co magnet
Sm-Co is actually a type of nickel sealing and is exclusively meant for those magnets that are employed in medical procedures. Every magnet piece consists of iron flakes and it will be released with the magnetic force. When such magnetic force is allowed to penetrate into the body, there are chances that it will destroy or even sterilize the necessary chemicals in the body, along with some contaminants.
By coating the magnets employed in medical procedures with Sm-Co nickel coating, the iron flakes in the magnetic field will be restricted from entering into the human body. The coating will also make the surface area of magnets tougher and hence amplifies the effect of magnetic force as required to cure any disorder.
Is it necessary to coat all Nd-Fe-B magnets
Neodymium magnets are one of the rare earth magnet types available in today’s world. From the time they are extracted from the earth’s crust, research is conducted so as to improvise the magnetic force. The improvisation in magnetic force will help many fields to make use of them to the fullest.
Since Nd-Fe-B contains iron as one of the basic metals, it is more prone to corrosion, rusting and even damage in the chemical structure. Hence, while producing this magnet, the manufacturers make use of better powder mixing procedure, so as to increase the strength of iron in it. The tougher the iron is, the lesser they are prone to external damages. So it is not necessary to coat all magnets, if they are produced using better-powder-blending procedure.
What exactly is the difference between nickel and aluminum coating
There are many differences between the usage of nickel or aluminum as coating material for magnets.
Since aluminum has soft chemical properties when compared to nickel, it is used only to protect the outer surface of magnets from the external influence. The coating or plating on a magnet should be one that not only protects the magnet from external influence, but will also form thick bond with the magnetic field. Hence, experts use both the material as per the preference.
Autoclaving of magnets – know about the right protection coating for magnets
The autoclaving will be done for different magnet types at different milliTorr levels. If it is a simple level, then the regular magnets can hold the effect. If the efficiency increases, then there are chances that the bonded materials start breaking off. Hence, it is not suggested to autoclave the magnets that are already bonded with other metals.
There are many things that will help you understand about coatings and plating for a magnet. For more information, visit usneodymiummagnets.com.