Managing The Risks Of SCM Failure
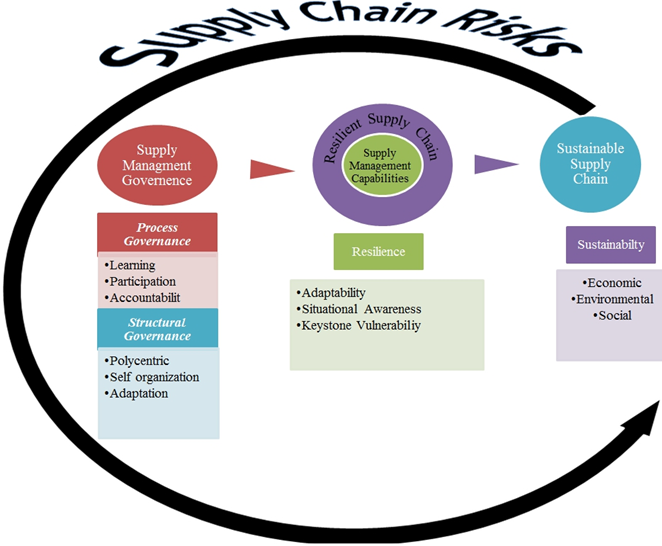
A company’s supply chain experiences more risks than any other department does. The main reason is the global design and intrinsic impact of financial performance. For any supply chain dealer, risk is quite natural, as there are innumerable forces in the field. One may experience challenges in safety and quality, shortage in supply, environment damages, legal issues, new regulatory compliance, and natural disasters. There is higher chance of risk with the global supply chain, more time required for global supply, different customs, supply slowdown, and warehouse congestion. Any instability in the political atmosphere of the operating country also affects economy, and exchange rates affect livelihoods.
In supply chain, formal documentation is required for managing risks. Even if businesses have not faced crises, risk management should be priority. In spite of the high amount of research conducted, seminars held, and papers written on supply chain, companies seem to be precarious when it comes to the ability to predict.
Companies feel these are the primary risk concerns are:
Loss of facility and no plans about backup
In the event of a major failure of equipment or a natural calamity, the company shuts down. However, most companies either have backup planned to be installed almost immediately. But, for those who do not run on adequate backup for their facilities, it is a major concern.
Companies don’t understand how to save business and meet customer demands with product substitution, inventory, and practical communication. They need to have a response plan documented for any kind of disaster to mitigate risk in the supply chain.
Loss by suppliers and plans of backup
Most companies are not adequately equipped to supply within a stipulated period. Unforeseen disasters add to the risk. Long supply chains come with more risk. There is wide variation in firms having solely sourced suppliers: a firm may be sole sourced yet in a broad area. Although many firms work with sole sourcing, they have their reasons for taking the risk. Some do it because of lesser cost, some base it on quality, or the supplier understands their specific needs, while some may attribute it to long relationships and trust factors.
Value chain risks
One primary risk that lurks in the minds of businesses is quality. If supply lines are long, it becomes increasingly tough to solve quality issues. Longer supply globally also calls for increased inventory, maintaining which can be equally risky. Many US companies prefer to keep more than 75 days of supply in another inventory while outsourcing to Asian countries. Some 20 years back, when companies explored the Asian industry, inventories weren’t a big concern. As the number of inventories increased, those who did not understand its impact faced huge dismay as the supply chain was long and global.
Moreover, there are natural disasters and manmade destructions like piracy, terrorism, etc., which delay the supply chain process and optimization. Of course, with experience, firms are learning a lot more on how to save their products from such issues.
The basic way to counter risks in supply chain, and planning, is to choose suppliers who are competent, globally acknowledged, and financially strong. Studies show it takes almost two years before a globally certified supplier can be developed. Hence, while businesses are on the process of developing competent suppliers, it is imperative they keep strict vigilance on their actions and evaluate all kinds of risks they may face during their supply chain management.