The Importance Of Managing Spill Control Stations Effectively
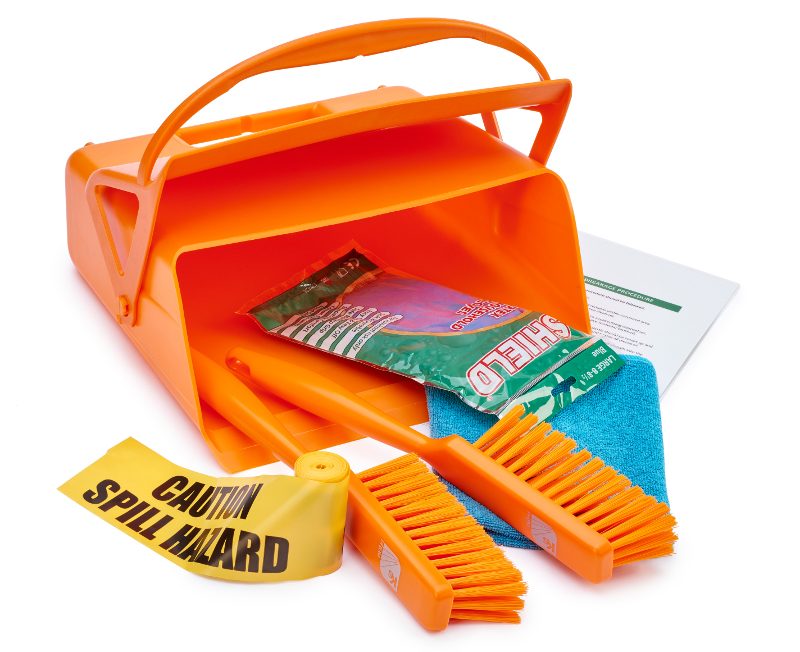
Glass breakages and allergen spills require handling in similar ways and to manage your spill control station effectively, you first need to have robust procedures in place for dealing with these types of incidents. You should also have risk assessments in place for all eventualities where spills can occur. Try and identify vulnerable areas and be clear on the risks to customers if they come into contact with breakages and allergen spills. Minimise the risk and you’ll minimise any possible repercussions.
For efficient and effective clean up, you’ll need a well maintained spill control station. Clean up as quickly as possible using the right tools for the job – these should be colour coded for ease of use.
Sanitise the area and get it checked by a supervisor if necessary, then fill out an incident report if required, so you have a clear chain of accountability.
Good training is essential for the effective management both of spill control stations and any incidents that occur. Ensure that all staff know exactly where clean up kit is located and how it should be used. You’ll minimise downtime and any negative impact, and speed up your procedures if you familiarise staff with the response routine.
Having a spill protocol and a well-equipped spill control station is vital for allergen control and to stop cross-contamination, particularly in a warehouse or manufacturing setting. In a warehouse, separating allergens into their own control area is often more achievable, but in a retail or manufacture setting this is not always the case. Spills can and do occur, and a swift response can minimise their impact.
While your staff are hunting for the appropriate clean up kit, you’re losing out on productivity. The simplest way to minimise downtime from breakage and allergen spills is to manage your spill control station in an effective manner. Ensure everything is clearly labelled and that employees are aware of what different colour coded clean up kits are intended to deal with. Build regular inspections of supplies into your business practice and put in place clear procedures for re-ordering exhausted supplies.
You’ll need a range of equipment and it’s often most cost effective to buy in kit form. This makes for easy storage and accessibility; thanks to the way some kits are colour coded. Ensure that the cleaning kit is thoroughly sanitised and correctly stored after each incident.
For storage purposes, we recommend the use of shadow boards that can be personalised with your company logo. These are a clever way of ensuring that there is always a designated place for your equipment. In the event of a spillage, employees can simply grab and go and then return the equipment ready for next time.
Managing your spill control station effectively will minimise risk, improve productivity and mean you are well equipped to deal with any situation!