Cooling Tower Chemical Treatment: Processes and Their Importance
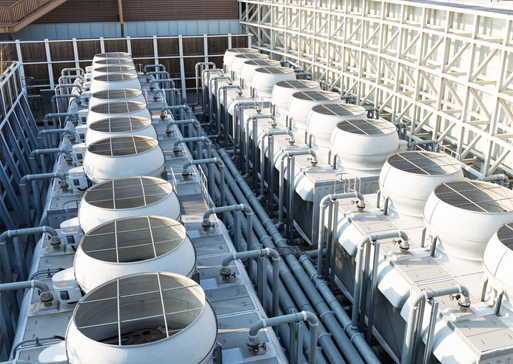
Industrial cooling water systems are subject to several potential problems:
For corrosion to occur, a galvanic cell must be present, with an anode and a cathode. This is usually a result of irregularities in the material surface or stress damage. The anode corrodes and metal is lost, deposited elsewhere in the system.
Zinc may be used as a cathode inhibitor, combined with phosphonate as an anodic inhibitor, preventing unwanted zinc deposits. If zinc is inappropriate for cooling tower chemical treatment, phosphate held in a polymer dispersant provides an alternative. The phosphate is an anodic inhibitor, whilst the polymer helps prevent calcium phosphate build-up causing blockages in pipes and heat exchangers.
Inorganic phosphate treatment is generally used for more aggressive waters and organic phosphate solutions reserved for less aggressive media, where they could lead to increased corrosion of mild steel.
Scale forms when sludge or mineral particles are deposited on surfaces. Mineral particles are generally introduced from external sources, such as water quality or air pollution. Sludge particles are usually from microbial growth or corrosion products. Polymer treatment can prevent or reverse scale formation, whereas surfactants change the surface properties of the suspended particles, leaving them less adherent.
Treatment for biological growth inhibition will be dependent on the type of microbe identified, the volume of water to be treated and the pH of the water. Enzyme poisons penetrate and inhibit the metabolic activity of enzymes. For example, cell respiration resulting in oxidation reduction. Oxidizing biocides, such as chlorine, oxidize cell protein groups, resulting in an inability of the enzyme to respire. Non-oxidizing biocides may be used in conjunction with oxidizing biocides, to ensure fully effective treatment of all enzymes. Cell wall toxicants adhere to the walls of the enzyme cells, preventing the absorption of essential nutrients for the cell. Relatively high concentrations of the toxicant may be required, compared with other treatments.
Cooling water towers provide excellent breeding conditions for Legionella bacteria. Should droplets of water, contaminated with the bacteria, be breathed in, it could cause a potentially fatal form of pneumonia, Legionnaire’s Disease. There have been several cases of such incidents, involving cooling water towers, reported in the media in recent years. A combined oxidizing and non-oxidizing biocidal treatment is effective against the risk of Legionella.
Appropriate chemical treatment of cooling water towers can help prevent equipment failures, improve efficiency and protect public health. A proper programme is a priority for any responsible operation.