Understand The Marvelous Process Of Making Rare Earth Magnets
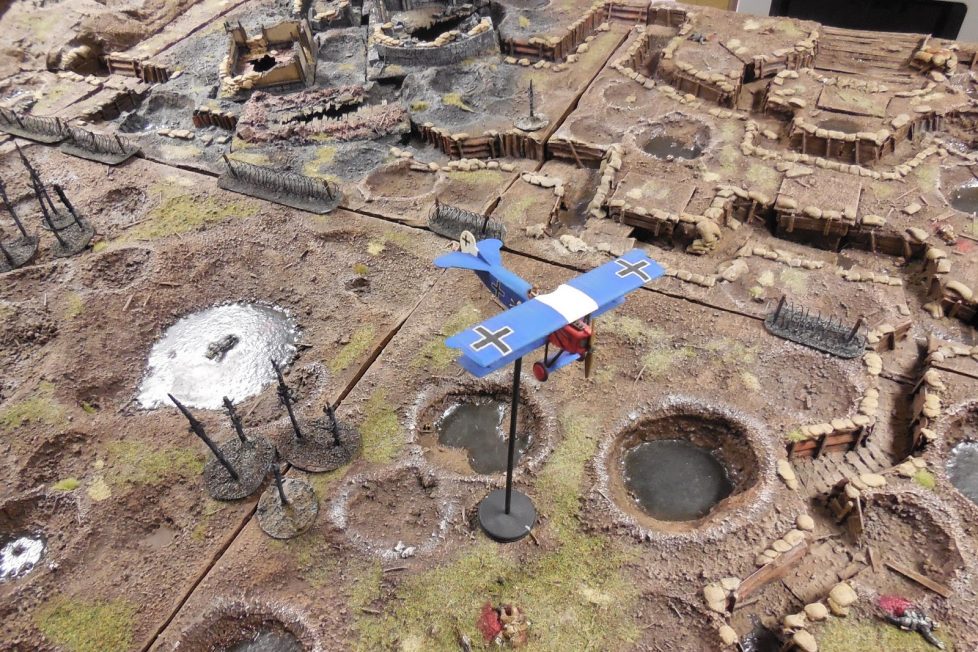
Rare earth magnets developed in ‘70s and ‘80s are the strongest permanent magnet made from earth alloys.
Different kinds of rare magnets –
US neodymium magnet are the strong kind of lasting magnet commercially available in the market. They have replaced many kinds of magnets. Today, they are used in myriads of applications like hard disk drives, cordless tool motors, magnetic fasteners, MRI, electric motors, electric generators, and more.
The rare factor related to this magnet is its potent force field, which can attract power 1000 times more than its weight. Rare earth magnets differ in quality. The strength of end product depends on the kind of rare earth used and the manufacturing process.
Neodymium magnets unparalleled strength is possible because of highly developed and subtle arrangement of electronic elements and the rotation of their electron. The process of making neodymium magnet is a technological marvel.
Manufacturing process of rare earth magnets
License is needed to produce rare earth magnets, especially neodymium ones.
Mining
Rare earth elements like Praseodymium and Neodymium available from the earth are ferromagnetic. It means they can be magnetized permanently like iron, when mixed with transition metals like iron, cobalt, and nickel, which come from the earth.
Grinding & mixing the alloy
Rare earth elements are alloyed with ferromagnetic materials in different proportion. The necessary materials are grinded in powder form and mixed in variety of proportions to create a new material with a range of magnetic properties. Some magnets are strong, while others are more durable or can endure high temperature.
Pressing or compacting the powder
The mixtures is placed in cavity tool then compressed
Particle alignment
Just before compressing, alignment field is employed to optimize the ferromagnetic mix for magnetization.
Sintering
After the pressed parts are aligned they are loaded inside a vacuum sintering kiln that locks the materials firmly in place.
Milling & cutting
After sintering the large block magnets are further refined by milling, grinding, and cutting into small, smooth pieces.
Plating or coating
After attaining the final shape, the magnet has to be coated for protection from corrosion, especially neodymium magnets.
Charging and magnetizing
After the processes of sintering and plating the magnet needs charging to generate an exterior magnetic field. Neodymium magnets only get magnetized in direction they were arranged for in alignment phase